Exploring the Principles of Welding Inspection: A Detailed Assessment of Procedures, Tools, and the Value of High Quality Control in Welding Industries
Welding examination serves as a foundation in the maintenance of safety and security and architectural honesty across various sectors. By checking out the essential procedures and tools made use of in these evaluations, one can value the complex balance in between quality assurance and conformity with well-known standards from organizations such as AWS and ANSI. The methods used, including aesthetic and non-destructive testing strategies, are critical in discovering imperfections that could endanger the toughness of bonded structures. Understanding the implications of these techniques elevates important inquiries regarding their efficiency and the future direction of quality control in welding.
Significance of Welding Examination
Welding assessment plays a crucial function in making certain the stability and safety of welded structures. It acts as an organized strategy to examining weld quality, recognizing prospective issues, and ensuring conformity with established requirements and specs. The relevance of welding assessment extends past mere adherence to regulations; it is essential in safeguarding human lives and shielding financial investments in infrastructure.
Defective welds can cause devastating failures, leading to substantial economic losses, injury, or loss of life. Strenuous inspection procedures are crucial to spot problems such as insufficient infiltration, porosity, or fractures before they intensify into critical failures. Additionally, effective welding assessment contributes to the total efficiency and durability of structures, guaranteeing that they can stand up to the problems for which they were created.
In addition, the application of welding evaluation promotes a culture of quality and liability within the welding market. By prioritizing inspection, organizations demonstrate their dedication to quality, consequently improving their track record and competition in the market. Eventually, welding examination is not merely a step-by-step action yet a fundamental component of design honesty and safety assurance, vital for the effective implementation of welding projects across numerous fields.
Secret Inspection Processes
A comprehensive approach to welding examination involves several essential processes that are necessary for ensuring weld high quality and architectural honesty. The initial essential process is aesthetic examination, which allows assessors to recognize surface area defects such as cracks, porosity, and incorrect bead appearance. This method acts as a preliminary analysis to make sure that the weld meets specified criteria.
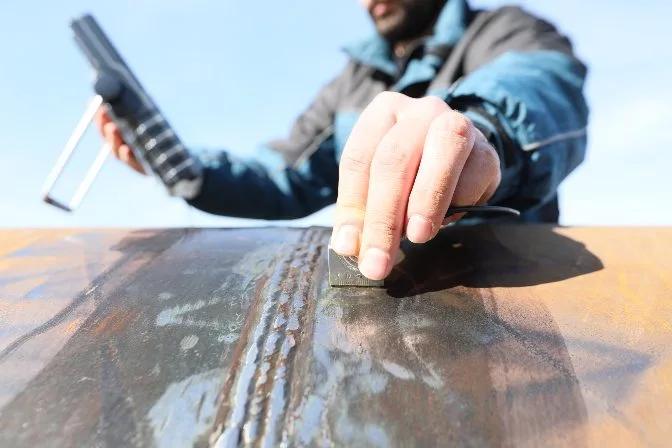
Furthermore, harmful screening might be performed on sample welds to analyze their mechanical properties and efficiency under stress and anxiety. This process entails influence, tensile, and exhaustion screening to verify that the weld can stand up to functional conditions.
Lastly, paperwork and coverage are critical parts of the inspection process. Preserving accurate documents of examinations, monitorings, and examination results helps make sure conformity with industry standards and assists in regular improvement in welding practices. Collectively, these vital processes form the backbone of effective welding assessment and top quality assurance.
Tools for Weld Analysis
Countless devices are essential for reliable weld analysis, each made to assess different aspects of weld high quality and performance. Amongst one of the most widely made use of are visual examination devices, including magnifying glasses and borescopes, which allow assessors to recognize surface problems such as cracks, porosity, and improper combination.
Furthermore, ultrasonic screening (UT) tools is critical for identifying interior defects. This device uses high-frequency acoustic waves to expose interruptions within the weld, making sure the stability of the product. Radiographic testing (RT) tools, which use X-rays or gamma rays, in a similar way give insight into the internal framework of welds, enabling the recognition of additions or voids.
For specific dimensions, calipers and gauges play a substantial function in determining weld dimensions and ensuring adherence to defined tolerances. Hardness testers evaluate the mechanical residential properties of the weld, ensuring it fulfills efficiency requirements.
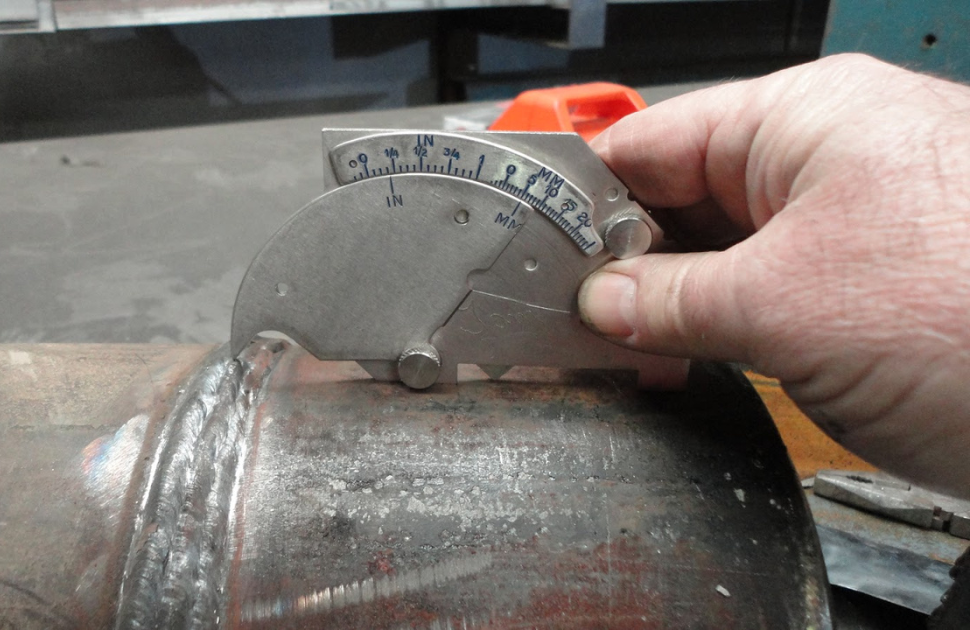
Methods for Examining Quality
Just how can the high quality of welds be dependably evaluated? A selection of methods are employed to examine weld integrity and guarantee adherence to defined criteria.
Ultrasonic testing (UT) is another prominent method that makes use of high-frequency sound waves to spot inner defects within the weld. Houston Welding Inspection. This method provides a comprehensive sight of the weld's integrity without endangering its architectural stability. In addition, radiographic testing (RT) employs X-rays or gamma rays to expose internal defects, using in-depth understandings into weld high quality
Magnetic fragment testing (MT) works for identifying surface area and near-surface discover this info here gaps in ferromagnetic products, making use of electromagnetic fields and colored particles to highlight flaws. Dye penetrant screening (PT) can be employed to uncover surface-breaking defects by using a color that permeates into cracks and is subsequently revealed.
Conformity With Sector Requirements
Compliance with market standards is important for ensuring the top quality and safety of bonded structures. These requirements, established by companies such as the American Welding Culture (AWS) and the American National Specification Institute (ANSI), offer standards that control the welding process, products, and evaluation procedures. Sticking to these standards not only ensures the structural honesty of welds yet also mitigates risks related to failings that can bring about disastrous repercussions.

Welding examiners are charged with confirming conformity with these standards throughout the welding process (Houston Welding Inspection). This includes examining welding treatments, monitoring welder qualifications, and conducting detailed assessments of the last item. Non-compliance can cause substantial economic effects, task hold-ups, and damage to a firm's credibility
Routine training and updates on standards are important to keep employees educated and competent, making certain that all elements of welding procedures fulfill or exceed governing demands. Eventually, dedication to market criteria offers as a structure for quality in the welding see this here market, advertising safety and security and integrity in welded frameworks.
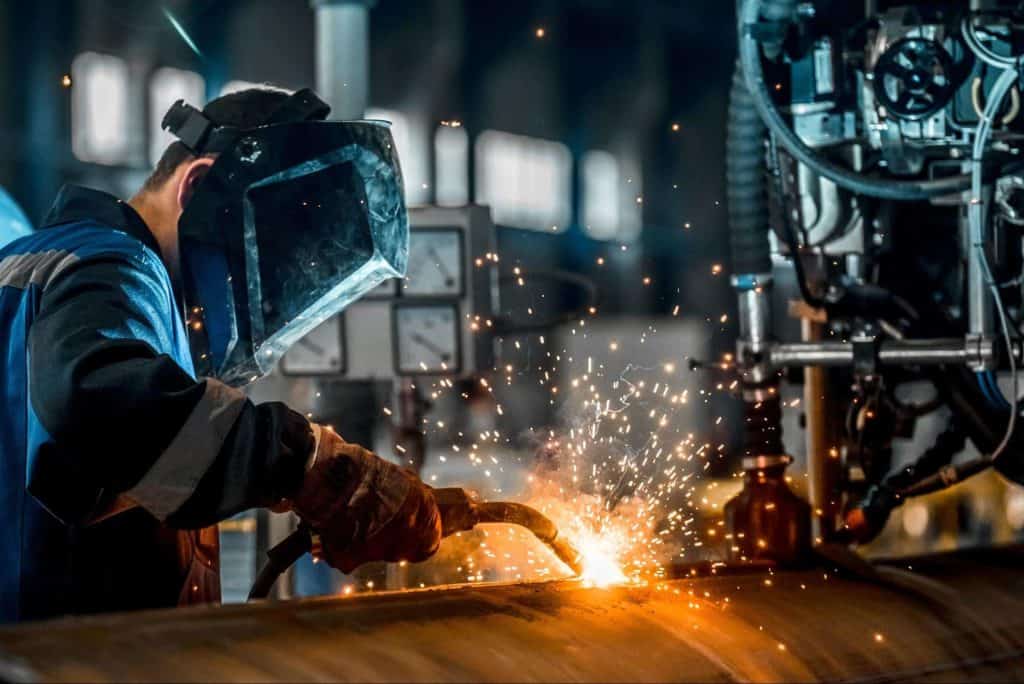
Conclusion
To conclude, welding evaluation offers as an important part in keeping the security and integrity of my blog bonded structures. With the execution of key evaluation processes and the application of sophisticated devices and techniques, prospective flaws can be determined and attended to efficiently. Adherence to industry requirements guarantees compliance and promotes a society of high quality within the welding industry. Inevitably, extensive assessment methods not just shield human lives yet likewise enhance the resilience and performance of bonded buildings.
Additionally, the application of welding evaluation cultivates a culture of quality and accountability within the welding industry. Ultimately, welding evaluation is not simply a step-by-step action yet an essential element of engineering honesty and safety and security guarantee, essential for the effective execution of welding projects throughout different markets.
A thorough technique to welding assessment entails a number of vital procedures that are vital for making sure weld top quality and architectural honesty. These requirements, established by companies such as the American Welding Culture (AWS) and the American National Criteria Institute (ANSI), provide standards that control the welding procedure, materials, and inspection procedures.Welding assessors are charged with verifying compliance with these requirements throughout the welding process.